Nowadays, with the rapid development of science and technology, people have higher and higher requirements for molds. The computer CAD system can be said to be dedicated to injection molds, because for molds, the most important thing is to be able to fill the mold chamber in the later stage and have uniform stress distribution. Therefore, it is necessary to use CAD system functions to carry out two-dimensional and three-dimensional design of products, and perfectly integrate the quality and design of molds. So how to design the mold in order to further optimize its quality? Here is the answer from Xiaobian.
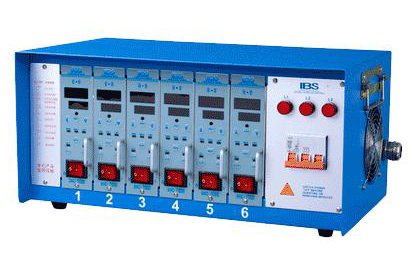
1、 Special for injection mold: the design of final forging and pre forging die chamber will optimize the quality
[1]、I-section pre forging die bore design
The design of the preformed die bore of the I-shaped section of the connecting rod is mainly to control the cross-sectional area of the I-shaped part to be slightly larger than that of the corresponding final forging, but it must be controlled within 2% - 5%, and the complex connecting rod must be controlled within < 2%. Otherwise, not only the I-shaped part will be folded, but also too much metal will flow violently in the die bore, increasing the wear of the die bore.
[2]、Design of gear pre forging die chamber with wide and thin web
During die forging, the metal in the web plate flows outward very violently, which is easy to fold inside the rim. At the same time, due to the thin web plate and great deformation resistance, the spoke of the die chamber is subject to great friction, which will wear out quickly and the die life is low. In addition, because the spokes are very thin, the temperature drop is fast, which increases the deformation resistance, increases the wear of the mold, and accelerates the failure of the mold.
[3]、Design principle of pre forging die chamber
In the design of pre forging die bore, not only the distribution of cross-sectional area and volume of pre forging and final forging should be considered, but also the relationship between the height and width of pre forging die bore and final forging die bore must be determined. For the mechanical press, the pre forging is designed as upsetting forming in the final forging die bore as far as possible, but for the final forging that is not easy to fill or easy to produce creases, extrusion forming is adopted. These principles should be designed according to the shape characteristics of different forgings. Practice has proved that the design of pre forging die chamber is reasonable, and the service life of forging die can be increased by 30% - 50%.
The pre forging die chamber is used to improve the flow conditions of metal when filling the final forging die chamber, avoid folding and insufficient filling defects on the forgings, ensure the stability of the forging process, reduce the metal deformation of the final forging die chamber, reduce the wear of the die chamber, and improve the service life of the whole forging die.
2、 Special for injection mold: the ingenious design of mold structure will optimize the quality
In order to make the forgings well filled and the stress in all parts of the die balanced, it is necessary to make a reasonable blank, so as to meet the requirements of the cross-sectional area and volume of the forgings, and obtain the shape and size close to the calculated blank drawing. If the shape and size of the blank are designed unreasonably or the blank die bore is seriously worn, the service life of the pre forging die and the final forging die will be reduced.
In a word, the two-dimensional and three-dimensional design of CAD system is special for injection mold. The specific design factors still depend on the final forging and pre forging mold bore design, as well as the structure of the mold itself. Only when the process design of the mold is in place can the quality of the mold be improved. I believe that according to the above Xiaobian's description, you will also have a certain understanding of the mold industry and become better familiar with the mold industry.